Maximizing Electric Aircraft ROI Through Advanced Materials Innovation
| 6 min read
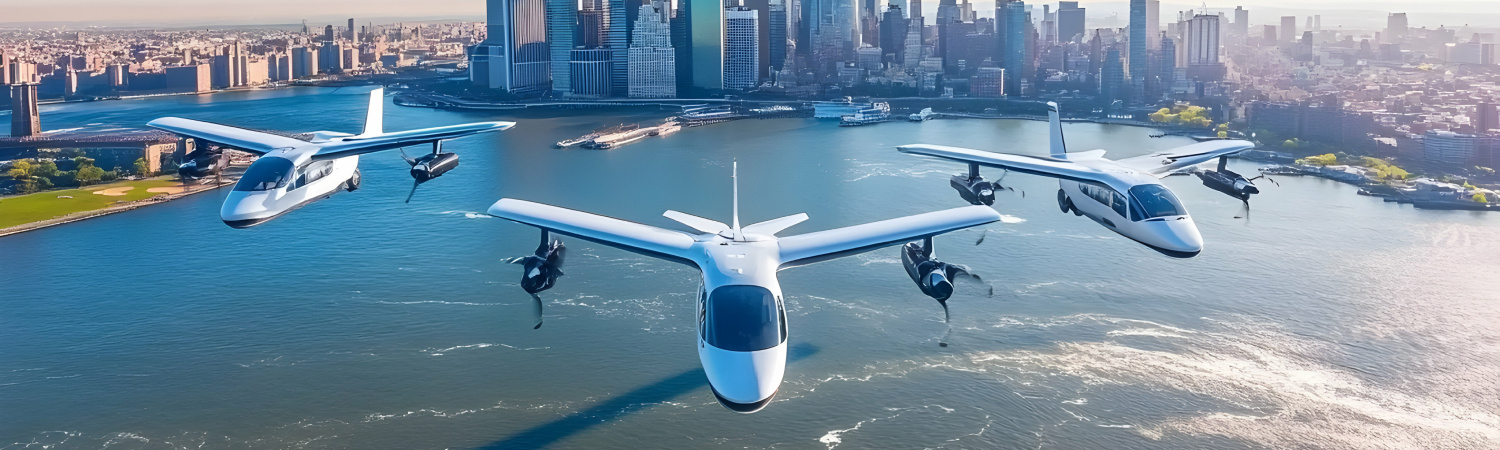
The economics of electric aircraft are fundamentally tied to their design and material choices. As the industry accelerates toward electrification, manufacturers and operators discover that advanced materials — particularly in motor components — aren't just a technical consideration but a critical driver of business performance and profitability. The selection of optimal materials early in the design process can create competitive advantages that compound throughout an aircraft's operational life.
The Business Case for Electric Aircraft
Electric aircraft represent more than just a sustainable alternative to conventional aviation. Their success hinges on delivering compelling economics across urban air mobility, regional transport, and commercial applications. While battery technology often dominates the conversation, the other major subsystems of the powertrain are equally important. The battery, the inverter, and the electric motor each incorporate advanced materials for optimal performance. The market opportunity is substantial - by 2030, demand for electric aircraft is projected to reach $37 billion annually, with over 5,000 units forecasted for urban air mobility alone.
Watch Video: The Motor Putting the Electrification Revolution in Motion
Advanced Materials Increase Power Density and Improve Performance Metrics
In the drive to higher performance systems, designers focus on improving the power density of motors. Material selection plays a critical role in achieving high power density. Advanced magnetic materials, like Carpenter Electrification's Hiperco®iron-cobalt alloys, particularly in electric motor components like stator and rotor stacks, create a cascade of performance benefits that directly impact the bottom line. These improvements compound across entire fleets, creating significant competitive advantages for operators who optimize their material choices.
A Closer Look at Power Density Advantages
Advanced materials like Hiperco® alloys enable higher power density motors that deliver up to 30% more power in the same footprint. These advanced soft magnetic materials also improve motor efficiency by up to 3%, reducing heat generation and cooling system requirements. These improvements allow aircraft designers to reduce motor size while maintaining performance or increase available power without weight penalties. These improved propulsion systems increase the aircraft's payload capacity and range.
Payload Capacity Benefits
The aircraft design process presents many trade-off decisions, and motor designers typically target a fixed budget for weight and volume. The high magnetic saturation and permeability of Hiperco® increase the propulsion units' power density and torque density by 20 - 30%. This generates more lift and thrust with the same motor weight and volume profiles. This translates to increased payload capacity — in many electric vertical takeoff and landing aircraft (eVTOL) designs, the maximum take-off weight (MTOW) increases to an additional passenger seat. Whether in urban air mobility or cargo applications, this extra capacity directly increases revenue potential per flight.
Read Blog: Maximizing eVTOL Motor Performance - From Materials to Manufacturing
Range Extensions
Performance data across multiple eVTOL configurations demonstrates range improvements of 12-30% (depending on the eVTOL model) through Hiperco®-based electric motor integration. For regional mobility applications, these extensions enable new route possibilities and improved operational flexibility. The enhanced range also provides crucial safety margins and reduces the need for energy-intensive reserve capacity, further improving efficiency.
Transforming Performance into Profit
The financial impact of these performance improvements is compelling. Analysis of typical eVTOL operations reveals how material-driven enhancements translate into revenue across various operational scenarios:
Additional Passenger Revenue
With average flight lengths of 25 miles and 25-40 daily flights at 90% utilization, a single additional passenger seat can generate up to $1.1 million in annual revenue, assuming only 50% occupancy of that extra seat. Over a 10-year service life, this represents over $10 million in incremental revenue per aircraft. For fleet operators, this revenue multiplies across each vehicle in service.
Operational Cost Savings
Beyond direct revenue, improved power density and efficiency reduce energy consumption and cooling requirements. Electric motors using Hiperco® stator and rotor stacks can operate at lower temperatures, reducing cooling system complexity and weight. These improvements compound across large fleets, creating meaningful operational cost advantages through reduced energy consumption and simplified thermal management.
Private Access: Hiperco® 50 Datasheet Interactive Dashboard
Maintenance Considerations
Higher-performance materials often demonstrate superior durability and thermal management, potentially extending service intervals and reducing maintenance costs. Lower operating temperatures reduce component stress and degradation rates. This impact grows significantly as fleet sizes increase, reducing maintenance requirements and creating substantial cost savings over the aircraft's operational life.
Real-World Performance Data
The benefits aren't theoretical. Modeling across multiple eVTOL configurations shows consistent improvements, including the following:
- Multi-copter designs: Up to 18% payload increase or 19% range extension
- Tilt-rotor configurations: 24-26% greater payload capacity or 17-30% longer range
- Lift-plus-cruise aircraft: 21% payload improvement or 12% range increase
These gains allow operators to optimize their aircraft for specific mission profiles, whether prioritizing payload, range, or a balance of both.
Download Resource: Advanced Materials for Electrification Guide
Future Economic Implications
As the electric aircraft market matures, the economic advantages of advanced materials such as Hiperco® stators and rotor stacks will become increasingly critical. With annual eVTOL demand projected to reach 5,000+ units by 2030, manufacturers who optimize their designs for performance and profitability through materials innovation will capture dominant market positions. Early adopters of advanced materials technology will benefit from significant competitive performance and advantages in operating economics.
Accelerating Your Electric Aircraft Innovation
Advanced materials innovation is the path to profitable electric aircraft operations. With over 134 years of specialty alloy expertise and a deep understanding of electric motor stack manufacturing, Carpenter Electrification delivers the materials technology needed to optimize aircraft performance and maximize return on investment.
Ready to explore how advanced materials can transform your electric aircraft? Connect with one of our experts to discuss your specific performance requirements and discover solutions to deliver measurable improvements to your bottom line.