Advanced Techniques for Enhancing Electric Motor Performance and Efficiency
| 7 min read
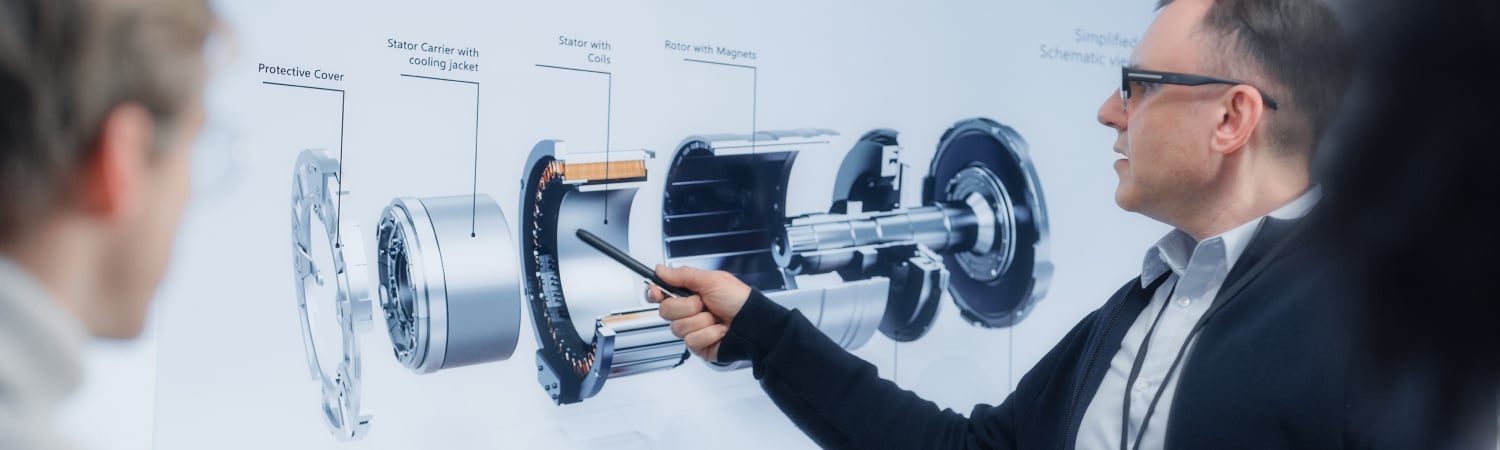
The electric revolution demands motors that deliver maximum performance within increasingly challenging constraints. Whether you're designing for aerospace, automotive, or industrial applications, the fundamental question remains: How do you optimize your motor for the specific demands of your application?
Do you need increased torque within a restricted volume? Are you looking to extend vehicle range through improved efficiency? Or perhaps you need to reduce motor size while maintaining performance? The answers lie in material selection and implementation expertise.
Key Performance Parameters in Electric Motors
Successful electric motor design requires balancing three critical parameters that define performance in electrified applications.
Power Density Requirements
Power density — the ratio of power output to motor volume — has become the north-star metric for next-generation motor designs. Higher power density translates directly to system-level benefits such as faster acceleration, reduced weight, extended range, increased payload capacity, and improved economics in weight-sensitive applications like aerospace.
Carpenter Electrification's Hiperco® soft magnetic alloys deliver up to 30% more power density than conventional electrical steels. This improvement creates a cascade of benefits throughout the system design, from battery sizing to thermal management.
Torque Specifications
Torque delivery determines how your motor performs under load —affecting everything from acceleration in EVs to precision in robotics. Traditional motor designs often struggle with torque-to-weight ratios, especially in space-constrained applications.
Our soft magnetic alloys offer up to 25% higher torque as a drop-in solution in current motor designs. This performance advantage doesn't require complete redesign—simply upgrading to Hiperco® alloys can transform existing architectures with minimal changes to manufacturing processes.
Motor Efficiency
Every percentage point of efficiency improvement in an electric motor translates to extended range, reduced battery requirements, and lower operating costs over the product lifecycle. In commercial applications, these efficiency gains are compounded into significant operational advantages.
With lower core losses, our soft magnetic alloys can increase motor efficiency by up to 3% — a substantial improvement in a field where engineers typically fight for fractions of a percent. These efficiency improvements directly impact system-level performance.
Related Blog: Guide to Electric Motor Optimization: From Design to Testing
Material Innovations Driving Motor Performance
The foundation of electric motor performance lies in material selection, particularly the soft magnetic materials used in stator and rotor constructions.
Soft Magnetic Alloys and Power Density Gains
Hiperco® alloys provide 25% higher induction, better permeability, and 30% lower losses than conventional electrical steel. These properties create options for designers to optimize their approach based on application priorities:
- Increase torque without altering your current motor design
- Increase power without re-sizing your motor
- Decrease your motor size without sacrificing torque
This flexibility allows engineers to focus on their specific design constraints rather than forcing compromises that undermine overall system performance.
How Material Selection Influences Torque
Torque production in electric motors is directly influenced by magnetic flux density. Hiperco® alloys achieve higher saturation induction (up to 2.4T), allowing motors to generate more torque from the same volume.
For design engineers, this creates opportunities to either boost performance within existing envelope constraints or maintain performance while reducing motor dimensions up to 30% — a critical advantage in space-constrained applications.
Core Loss Reduction
Energy wasted as heat in the magnetic core represents one of the primary efficiency limitations in electric motors. Our engineered soft magnetic materials minimize these losses through an optimized microstructure and precise processing.
The result is motors that run 10-20°C coolers during operation, offering better thermal management options and improved motor life. This temperature reduction compounds the efficiency advantages while simultaneously extending the components' lifespan.
Thermal Management: The Critical Fourth Parameter
While power density, torque, and efficiency receive the most attention, thermal management has emerged as an equally critical parameter in motor design. Heat generation limits peak performance and accelerates component degradation.
Our soft magnetic alloys address this challenge directly. Motors utilizing our materials run coolers at 10-20°C during operation, which is more than conventional designs. This temperature reduction provides several cascading benefits:
- Extended component lifespan
- Higher sustained power output
- Reduced cooling system requirements
- Improved reliability in high-temperature environments
This thermal advantage is helpful in weight-sensitive vehicles where the weight of the thermal management system must be minimized or those requiring sustained high-power operation.
Related Blog: The Features & Benefits of Soft Magnetic Alloys for Electronics
Measuring and Quantifying Performance Improvements
The advantages of advanced soft magnetic materials translate into measurable performance gains that impact both technical specifications and business outcomes.
Technical Specs and Business Impact
Our engineering partnerships deliver quantifiable improvements across key performance metrics:
- Power Density: Up to 30% improvement
- Torque: Up to 25% increase as a drop-in solution
- Efficiency: Up to 3% improvement
- Thermal Performance: 10-20°C cooler operation
- Size Reduction: Up to 30% smaller footprint possible without performance loss
These technical advantages translate to business benefits, including extended range, reduced battery requirements, lower warranty costs, and improved product differentiation.
Implementing Advanced Motor Optimization
Maximizing the benefits of high-performance soft magnetic alloys requires expertise beyond material selection. Processing techniques must be optimized for magnetic performance, dimensional tolerance, quality, yield, and production scalability.
Custom Solutions
Carpenter Electrification is a one-stop shop for laminations and stacks, with advanced, automated equipment and integrated processing from melt to strip and through stack assembly and test. Our team focuses on helping you realize your stator and rotor stack needs from prototype to serial production. We implement the best production method for your product based on the following:
- Unique performance requirements
- Design maturity
- Volume demands
- Process optimization for scale-up
Our decades-long expertise in specialized materials and stack processing offers unique high-performance stack solutions. Without expert knowledge of iron-cobalt stack processing, rotors and stators perform only marginally better than standard electrical steel.
Future-Proofing
The electrification revolution continues to accelerate, with performance demands increasing with each product generation. Partnering with Carpenter Electrification provides access to ongoing material innovations and processing improvements that keep your designs at the cutting edge of performance.
Our engineering team works alongside your designers to ensure the maximum benefits of high-performance soft magnetic alloys are realized for current products and your future roadmap.
Elevate Your Motor Performance
The path to optimized electric motor performance begins with material selection and extends through expert processing and implementation. Carpenter Electrification provides the advanced soft magnetic alloys and the engineering expertise required to transform these materials into high-performance motor components.
Whether you're looking to increase torque, extend range, increase payload capacity, reduce motor size, or improve thermal management, our tailored Hiperco® solutions create options for designers to optimize for their specific application needs.
Contact our team today to discuss your motor design challenges and discover how our soft magnetic materials can elevate your performance to new levels.