A Quicker Path to Market via Improved Stator and Rotor Testing Methods
| 4 min read
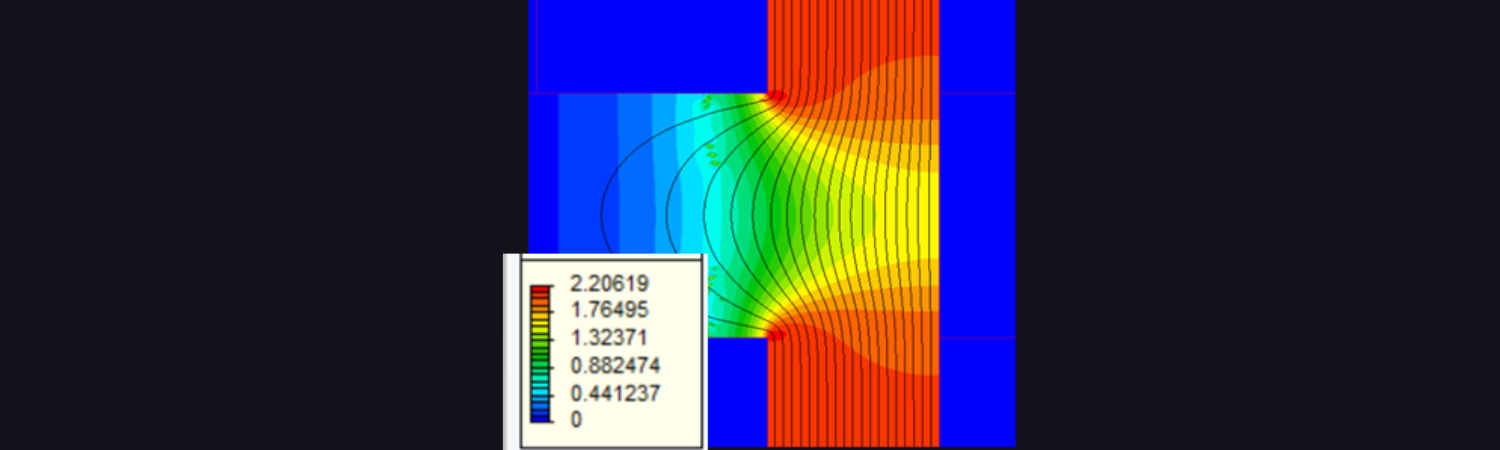
In the competitive world of electric motor manufacturing, efficiency and speed are crucial. In the competitive world of electric motor manufacturing, efficiency and speed are crucial to create a new design while quality and reliability become important at production scale. At Carpenter Electrification, we are committed to revolutionize the manufacturing process flow, incorporating our advanced stator and rotor testing methodologies for high performance electric motors using iron-cobalt alloy stacks.
Leveraging innovative techniques, we help motor designers achieve quicker market entry, improved product quality, and significant cost savings. Let's explore this in more detail.
Understanding the Limitations of Traditional Testing Methods
The traditional test methodology for iron cobalt stacks involves testing of loose laminations following ASTM standards. Iron cobalt stack manufacturing process generally involves alloy selection, lamination cutting, heat treatment, stacking, bonding, and finishing step and each process step impacts the stack responses significantly.
The traditional test process to some level covers the alloy selection and heat treatment portion of the manufacturing process. However, it does not cover the design specific impact of the cutting process along with the effect of bonding and finishing processes.
The Design-Prototype-Test-Redesign Loop
Since the present test process does not reflect the responses of the finished stacks, designers often rely on correction factors, assuming multipliers 1.5-2 x to approximate the finished product's performance. This leads to a cycle of prototype testing, redesigning, and retesting, which is both time-consuming and expensive. The inefficiency of this process can significantly delay the time to market.
Power and torque dense motors are used in applications where performance cannot be compromised. From our experience, most motor companies have taken more than three design iterations to reach the intended motor performance when relying on traditional test methods and correction factors. Some have taken as many as five. Given the time for the design, fabricate, assembly, and test loops this process routinely takes 12 – 18 months, and we have seen it stretch over two to three years.
Advanced Testing Methods for Stacks and Rotors
At Carpenter Electrification, we have developed improved testing methods that revolutionize the motor design process. Our approach involves testing actual finished stator and rotor stacks early in the design phase. This method provides accurate stack-level magnetics data, eliminating the need for speculative correction factors.
The Magnetic Testing Department within our Motor Technology Center (MTC) houses a variety of advanced stator and rotor test equipment. These systems directly measure magnetic responses of the stack at the back iron or tooth tips. Testing at elevated temperatures is also available for characterization.
Correlating modeled magnetic performance of a lamination design with actual 3D stack test data is complicated. Accuracy improves with experience. Our magnetics test technicians and applications engineering team have built an extensive knowledge base across a range of stator and rotor designs. The team collaborates with our customers on design iterations incorporating our models.
By incorporating advanced simulations and precise testing, we ensure that the performance of stator and rotor stacks is accurately determined during the prototyping process. This significantly reduces the need for multiple redesign loops, allowing for a more streamlined and efficient development cycle.
Benefits of Improved Testing Methods for Stack and Rotors
Embracing advanced testing methods offers numerous advantages for motor designers and manufacturers. As noted, our innovative approach provides accurate early data, enabling more effective development. Here are the key benefits:
- Reduced Development Time: An advanced stator and rotor stack testing methodology drastically cuts down the time required for motor development. Accurate data early in the process minimizes the need for multiple iterations. This streamlined approach accelerates the overall development timeline, enabling quicker market entry.
- Enhanced Quality Control: Consistent and accurate testing at the production scale is vital for maintaining product quality. Our methods help track stack quality throughout production, ensuring that each stack meets the highest standards. This leads to more reliable and higher-performing end products.
- Cost Savings: Reducing the number of redesign loops and minimizing uncertainties in the production process results in significant cost savings. Improved efficiency and reduced time to market help manufacturers achieve better financial outcomes.
- Superior Product Reliability: Focusing on precise and early testing speeds up the development process and enhances the reliability of the final product. End users benefit from motors that perform consistently and meet high-quality standards, fostering greater customer satisfaction and trust.
The Path Forward: Partnering with Carpenter Electrification
At Carpenter Electrification, we understand the challenges motor designers and manufacturers face. Our commitment to innovation and excellence drives us to provide solutions that enhance efficiency, reduce costs, and improve product quality. Partnering with us allows you to leverage our advanced stator and rotor testing methods to achieve quicker market entry and deliver superior products to your customers.
If you're looking to revolutionize your motor design and production process, contact Carpenter Electrification. Let us help you achieve a quicker path to market starting today.